4 and 5-Axis Milling in Fremont CA
If you’re looking for the ideal CNC machine for your purposes, you may pick between 4 axis and 5 axis CNC machines. Improved accuracy, faster setup times, and the capacity to build more complex components are just some of the benefits. When you think about CNC aluminum machining services, the word4 and 5-axis milling in Fremont, CA 5-axis CNC machining comes to mind.
Manufacturing success is dependent on selecting the right machining solutions. CNC machining, which is widely utilized in many industries, is used in almost all production processes. CNC (Computer Numeric Operate) refers to the use of a single or many computers to control a wide range of machine tools such as lathes, routers, and mills.
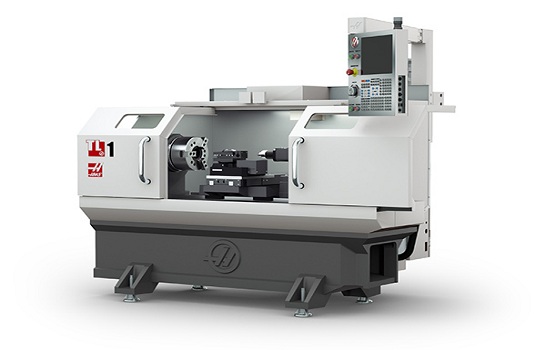
Using a 5-axis CNC machining technique, it is able to manufacture components and finished products from a wide range of materials such as plastics and metals with high precision4 and 5-axis milling in Fremont, CA
CNC technology may be used to manufacture a variety of materials, including plastics and metals.
When people hear about 5-axis CNC machining, their first thoughts are usually: high-tech, expensive, and difficult to run but 4 and 5-axis milling in Fremont, CA is easy to operate.Cutting equipment or different parts are moved across five different axes at the same time with the help of a computer numerical control system (CNC). Therefore, 5-axis CNC milling is so common in aerospace because it allows for the production of extremely complex parts. A major factor in the use of 5-axis CNC machines has been the desire to improve proficiency and reduce production time from the start of the process to its conclusion.
Another factor to consider is the capacity to rotate the table or cutting tool to prevent clashing with part-holding equipment. Rotating the table or cutting equipment to maintain the ideal incisive position and chip load can also help to improve machine life.
4 and 5-axis milling in Fremont, CAmachining is an example of CNC machining. We use a lot of 3-axis machining centers. The X-axis, Y-axis, and Z-axis of a machining center are together referred to as the 3-axis. Two rotating shafts will be added to the three traditional linear axes of X, Y, and Z in a 5-axis machining center. Two of the three axes of A, B, and C have unique motion modes in order to meet the technical demands of varied items.
5-axis machining opens us a world of options in terms of part sizes and forms. The term “5-axis” refers to the five possible paths that a cutting instrument can take. A 4 and 5-axis milling in Fremont, CA machining center’s cutting tool travels along the X, Y, and Z linear axes while rotating around the A and B axes, allowing it to approach the workpiece from any direction. To put it another way, all five sides of a component may be handled in a single configuration.
Four and five axis models CNC machining is used in many different product production scenarios. Depending on the one you choose, they may be utilized to make deep hole moulds, complicated 3D forms, and machine slanted surfaces without losing precision.
In terms of versatility, 4 and 5-axis milling in Fremont, CA5 is the best choice. It has risen to prominence in the manufacture of curved surfaces that are unsuited for 3-axis machining, such as impellers and turbine blades.
For a novice, knowing the difference between 4-axis CNC machining and 5-axis CNC machining is critical. This is the case since most CNC machines use 3-axis, 4-axis, and 5-axis CNC machining methods. This page outlines the distinctions between these three options.
Do you intend to employ one of the two approaches in your project? Which one, if any, is it? Take a peek at everything Rapid. Direct has to offer! Our CNC machining team is well-versed, and we can deliver high-quality products that suit your specifications. By using the link below, you can contact a member of the Rapid. Direct team or submit a quote request. We’re here to help you out.
Is your firm considering purchasing 5-axis CNC equipment? Alternatively, your firm may have already acquired the equipment but is still finding out how to configure and install it. Before making a purchase, a number of variables must be considered in order to get the most out of these super-productive machine tools4 and 5-axis milling in Fremont, CA
5 axis machining results in higher component quality, less work-in-process, and cheaper fixture costs. However, in order to reap these benefits, some new thinking is required.
4 and 5-axis milling in Fremont, CAMachining with five axes has several advantages
Single Setup
The requirement for several setups for 3-axis machines results in part misalignment, greater costs, and other problems. You can process complex forms in a single setup using 5-axis machining, increasing productivity, saving time, lowering costs, and eliminating operator error.
Shorter Cutting Tools
Shorter cutting tools can be utilized with 5-axis machining since the cutter head may be lowered and reoriented as needed. As a result, faster cutting rates may be achieved without putting undue strain on the cutters. Another benefit of shorter cutting tools is that they have less vibration. 5-axis machines produce a better surface polish since they have less vibration.
Complex
Complex components that would normally need casting may now be manufactured. Instead of waiting months for the casting to be done, your components may be made in a matter of weeks.
The tool’s durability
You may increase the tool’s cycle time and life by keeping the chip load consistent and the cutting position optimum.
The process of drilling a hole
Using a 5-axis machine, you may drill a succession of holes with changing compound angles quickly and efficiently. Each hole on a 3-axis machine would require a different configuration.
Avoiding a collision
In an inclined position, the tool holder isn’t in direct contact with the table or the cutting tool.